LTCC
Substrate Technology for Diode Laser Modules
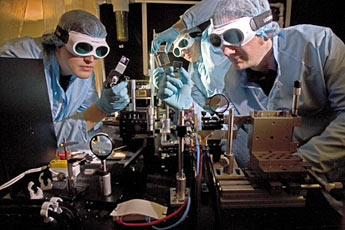
Lisa Daykin of GSI Ltd stated that “this
was a new and exciting technology that would
be extremely applicable to future products" |
In today’s global and commercial consumer
society, packaging is an essential and indispensible
part of a product’s design and the challenges
faced by packaging engineers should not be underestimated.
New electronic systems for automotive, communications,
medical, military and aerospace applications will
continue to challenge both packaging engineers and
technology due to the increased performance requirements,
higher densities, higher temperatures and limited
space available.
Low temperature co-fired ceramic (LTTC) technology
is known to be a cost-effective, adaptable, and
marketable solution to demanding packaging applications.
A particular challenge however, is in providing
cooling solutions to highly packed electronic and
optical components.
Under the direction of Professor Denis Hall, Heriot-Watt
University researchers responded to the need to
provide cooling solutions to highly packed electronic
and optical components by proving that green ceramic
tape (LTCC) could be laser machined to produce structures
for precise photonic applications, rather than the
previous emphasis on electronics.
An advantage of LTTC laminated manufacture is that
internal hollow structures can be obtained within
the non-porous, low expansion coefficient ceramic.
This process allows internal water-cooling of a
ceramic substrate for integration of high power
lasers. A programme to demonstrate cooling of the
industry-standard single BA emitter type of diode
laser has succeeded in showing the first use of
internal substrate cooling under a commercial diode
laser chip. This allowed the researchers at Heriot-Watt
to achieve low thermal impedance which is appropriate
for the next generation of laser chips with higher
power.
The future lies in integrating many lasers on a
ceramic “circuit board” supplying both
cooling and precise support for optical component
which will in turn allow products to be packaged
appropriately safeguarding the design inside. The
results of this project have attracted industrial
interest from GSI Ltd who use this kind of diode
laser in their portfolio of fibre lasers products.
A process patent has also been filed on the laser
machining of green ceramic tape. This resulted in
a dedicated CO2 laser-cutting machine for LTCC lamination
sheets in the Microsystems Group, designed and developed
by PowerPhotonic Ltd., joining a suite of other
equipments for the complete lamination and firing
of structures.
For more information contact:
Denis Hall d.r.hall@hw.ac.uk
0131 451 3081 www.lpa.hw.ac.uk/lpa_group.htm |