Cutting-Edge
Engineering Technology for Laser Machining of Zirconia
Ceramic in Dental Applications
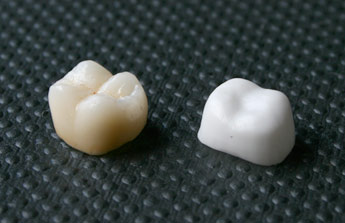
Nick Weston, Manager of Renishaw Edinburgh
stated “Renishaw has gained significant
benefit from working with The James Watt Institute
which has led to the formation of a strategic
alliance with Heriot-Watt University” |
The development and introduction of materials such
as ceramics in dentistry now provides patients with
a viable alternative to amalgams and the use of
non-precious metals. Yttria-stabilized Zirconia
is a particularly tough engineering ceramic. This
property makes it desirable for a wide range of
industrial and medical applications including bone,
tooth and joint implants, however it also makes
the material very difficult to machine in its final
state.
Computer-Aided Design (CAD) and Computer-Aided Manufacturing
(CAM) are already experiencing the fastest growth
in any area of dentistry, revolutionising restorative
dentistry, bringing a new level of productivity
and profitability to the production of crowns and
bridges.
Having established itself as the world’s leading
provider of in-lab scanning systems in recent years,
Renishaw has now applied this cutting-edge engineering
technology to its incise™ dental CAD/CAM system,
which combines high-speed 3D scanning capabilities,
powerful software and a new milling machine to allow
the manufacture of high quality zirconia crowns
and bridges.
Currently in dentistry, zirconia ceramic is processed
by mechanical means making this an extremely slow
procedure, typically requiring 3-6 hours of diamond
grinding to manufacture a single tooth crown. Alternative
methods of ceramic manufacturing are therefore required
to reduce cost and improve performance.
Collaborating with Renishaw Ltd, Duncan Hand at
the James Watt Institute for High Value Manufacturing
led a team to apply laser-based manufacturing processes
to the production of dental products.
The project led to the development of a laser machining
processes capable of high speed cutting of ceramic
components (up to 13 mm thick), followed by fine-scale
finishing removing surface cracks. The machined
parts meet the strength requirements of dental restorations,
and machining time is significantly reduced to approx
1 hour.
For more information contact:
Duncan Hand d.p.hand@hw.ac.uk
0131 451 3020 www.aop.hw.ac.uk |